Automated monitoring provides a reliable and cost-effective way to control construction noise and vibration, protecting project owners, construction companies, and nearby properties.
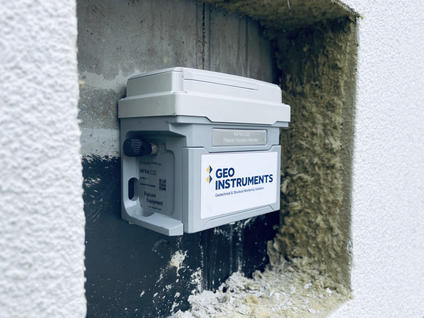
Common uses
Process
Automated vibration and noise monitoring can help avoid the property damage, delays, litigation and increased costs that can arise due to vibrations from construction activities such as blasting, rock excavation, general excavation, pile driving and tunnelling.
Monitoring equipment usually comprises:
- A triaxial geophone to sense particle motion
- A vibration monitor, also called a seismograph, to record and process signals from the geophone; and
- Software to produce compliance reports.
Additional hardware and services, such as weatherproof enclosures, solar panels, wireless data retrieval, smartphone alerts, and automated reports, can increase the efficiency and reduce the cost of monitoring.
Construction activities generate ground vibrations that propagate outward in waves, causing particle motion at the wavefronts. The velocity and frequency of these particle motions are the basis for most regulatory limits.
The vibration monitor continuously samples the three channels of the triaxial geophone, checking incoming values against limit thresholds.
At regular intervals, the monitor stores the peak particle velocity (PPV) value for each channel.
These values are used to generate a histogram report.
If any incoming value exceeds the limit threshold, the monitor records all of the incoming values for a few seconds. These values are used to generate a waveform report.
If the limit thresholds are exceeded, an alert is generated so that site engineers can take mitigating actions to bring vibrations within regulatory limits.
Histograms are used to demonstrate that the site has been actively monitored and that vibration levels have stayed within regulatory limits.
Waveform reports show the distribution of velocities and frequencies during exceedance events and are used for further analysis of the events.
Advantages
- High accuracy: Sensors and interfaces provide low noise, high precision, digitised measurements. Accuracy of 1.5m for every 32m SAA.
- Quick and easy to install: The SAA sensor can be inserted in a tight fitting PVC tube and held in compression to work. Once released, it can be pulled out and reeled back on its storage drum for reuse.
- Reliable: The rugged SAA sensor string is designed to be used in all fields of construction. The steel outer mesh provides protection while its rigid articulated segment chain design makes the SAA a sensor that can be used in most harsh environments.
- Robust: Wireless sensors and nodes can operate at temperatures from -40°C to +60°C.
- Intelligent: Segments can be disabled so that all relevant segments can feed raw data into an automatic processing protocol which distributes engineering displacement data to GEO-Instruments monitoring platforms.