These tests allow us to verify the actual bearing capacity of completed foundations. They are the only methods that help confirm whether a foundation has been designed and constructed properly, and therefore whether it meets the ultimate and serviceability limit state requirements.
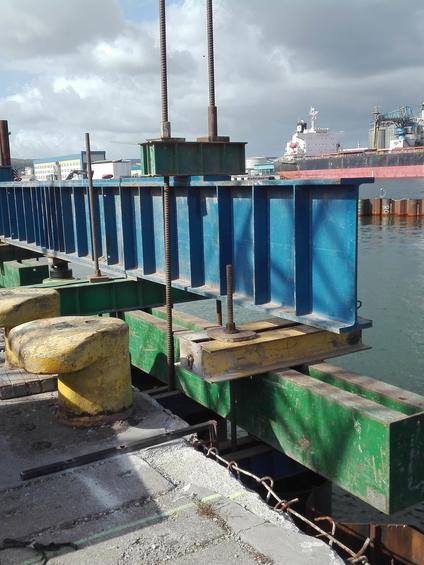
Common uses
Process
As the only company in Poland and one of only a handful in Europe, GEO-Instruments performs static pile load tests using the latest fully automated load-measuring kits that permit fully unattended static load tests while maintaining all technical standards and measurement accuracy standards. The remote load kits ensure maximum safety for the staff and bystanders alike, eliminating the need for hours of strenuous operation by a team of lab technicians, while at the same time providing a full real-time preview of the recorded results as well as the option to control and modify subsequent load factors.
Static load tests (SLT)
Static load tests (SLT) consist in progressively applying a specific force in a specified direction on a pile or column. Despite significant progress in developing advanced computational models and continuous development of special foundation technologies, static tests are still the most accurate method for verifying the bearing capacity and displacements of deep foundations in the ground. They permit checking the values of foundation displacements (settlements, elevations, shifts) with high accuracy and determining the permissible load values on their basis with great precision.
GEO-Instruments performs static tests based on national standards (e.g. PN-83/B-02482 and Eurocode 7) and foreign standards (e.g. ASTM), as well as on the basis of Detailed Technical Specifications and individual guidelines provided by designers and customers. Static load tests can be performed on practically any type of deep foundations, ranging from classic foundation piles (e.g. CFA or large diameter piles bored in recoverable lining pipes) through the latest technologies of displacement piles and columns (e.g. CSC and FCC columns) to gravel columns and diaphragm walls (e.g. barette piles).
Pile static test loads can be divided according to two main purposes, ie:
- Initial static test loads: used for design purposes (performed at the foundation design stage) are aimed at optimising the design or designing the most advantageous solution for a setting using foundation piles and columns as well as diaphragm walls
- Acceptance static test loads: used for acceptance purposes (performed at the stage of pile foundation execution or just after its completion), with a purpose to confirm whether or not the completed foundation meets the design assumptions. It is frequently one of conditions necessary for the acceptance of the completed foundation works.
GEO-Instruments performs each of these tests in all manners of technical execution available on the market, such as:
- Compressive load tests using adjacent anchor piles
- Compressive load tests with ballast
- Compressive load tests using a mixed method (anchor and ballast)
- Tension load tests
- Load tests for horizontal forces
Dynamic load tests (DLTs)
Dynamic load tests (DLTs) use the phenomenon of stress wave propagation, induced in the pile shaft by striking the pile head with a hammer with a weight corresponding to at least 1-2% of the pile’s bearing capacity. Stress wave propagation is recorded using sensors mounted on the concrete on the side of the pile shaft and connected to a portable data logger. The acceleration and strain (stress) recorded at the moment of striking the pile with a hammer permit determining the load capacity of the tested pile and the load-to-settlement relation using the analytical hammer - pile - soil model.
GEO-Instruments performs dynamic load tests based on the national standard PN-EN 1997-1-1 and foreign standards, in particular ASTM D 4945 Standard Test Method for High-Strain Dynamic Testing of Piles, as well as on the basis of the Detailed Technical Specifications and individual guidelines provided by designers and customers.
Dynamic pile testing eliminates the need for a time-consuming installation of steel retaining structure (static loads), which considerably reduces testing time as well as permits a free selection of test piles. The reliability of dynamic test results has been confirmed by many comparative analyses of static and dynamic tests.
GEO-Instruments uses dedicated CAPWAP (Case Pile Wave Analysis Program) software from Pile Dynamics, Inc. to analyse test results. The CAPWAP method utilises matching the return wave function, generated by the computational model of the buried pile, to the return wave measured during the dynamic test. The results of the CAPWAP method are the ultimate limit state per footing and per side surface as well as the simulated curve of pile settlement dependence on its load.
Advantages
Remote process control: Load tests are executed using fully automated load-measuring systems that permit much longer test loads than is the case with continuous service by an operator.
No power? Not a problem: Each automatic load kit is equipped with a high-capacity battery pack, which means that load tests can also be performed at locations where no permanent power source is available. The system can work efficiently for up to 14 days of daily operation on a single charge.
Data accessible from anywhere: Given that each load kit is equipped with a GPRS modem, recorded data are available virtually on the fly. With access to the Internet, the test load operator can track and control the test from absolutely anywhere. The data are sent to a secure server where they can be stored for archiving.
Automation under control: Our proprietary software controlling the automatic load kits permits full control over the load testing process. In case of non-standard situations, e.g. excessive pile displacement or dangerous movements of the steel retaining structure, the software alerts the load operator who then decides on further steps regarding the test.
Safety first: Conducting static load tests automatically eliminates the risk of operators performing analyses in the immediate vicinity of the retaining structure. Instead of hours spent on site, the operator can now control the test from a hotel room.